Formlabs Form 3+ Full Review
Formlabs, established by a group of MIT graduates in 2011, is well known for its SLA printers, which are widely used in industries like healthcare, product design, and engineering. With their Low Force Stereolithography (LFS) technology, Formlabs is popular with the resin 3D printing community. The Formlabs Form 3+ is a resin 3D printer built for industrial applications, with the capability to print proprietary silicone. This updated version of the Form 3 promises faster prints, improved part quality, and better material handling. For those accustomed to filament or traditional resin printers, the Form 3+ introduces new possibilities with silicone-based applications. In this Formlabs Form 3+ full review, we’ll explore its features, technology, and capabilities with silicone printing, comparing its performance with its 3D printer siblings on the same line.
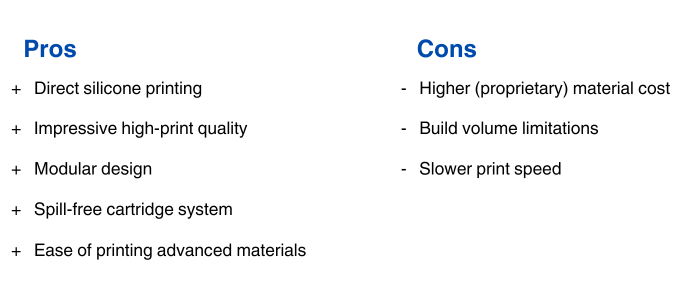
Design and Build Quality
Built for Precision and Specialized Silicone Printing
The Formlabs Form 3+ has the capability to print directly with Formlabs’ proprietary Silicone 40A Resin. This is a unique advantage in the field of resin 3D printers. Unlike many other machines that rely on silicone-like alternatives or indirect molding methods, the Form 3+ uses Formlabs’ patent-pending Pure Silicone Technology™ to create 100% silicone parts. The fully enclosed design ensures a stable, controlled environment for producing precise and durable silicone prints. This printer’s modular design and spill-free, swappable cartridge system make it easy to switch between materials. Users benefit from a clean, efficient workflow when working with this specialized material, as well as other validated materials in the Formlabs ecosystem.
Optimized for Direct Silicone 3D Printing
The Form 3+ integrates Low Force Stereolithography (LFS) technology, which reduces peel forces. This enables precise and reliable prints with flexible materials such as silicone. The Silicone 40A Resin has excellent flexibility and durability, with properties such as a 40A Shore durometer and 230% elongation at break. This is ideal for industrial applications where pliability and strength are key.
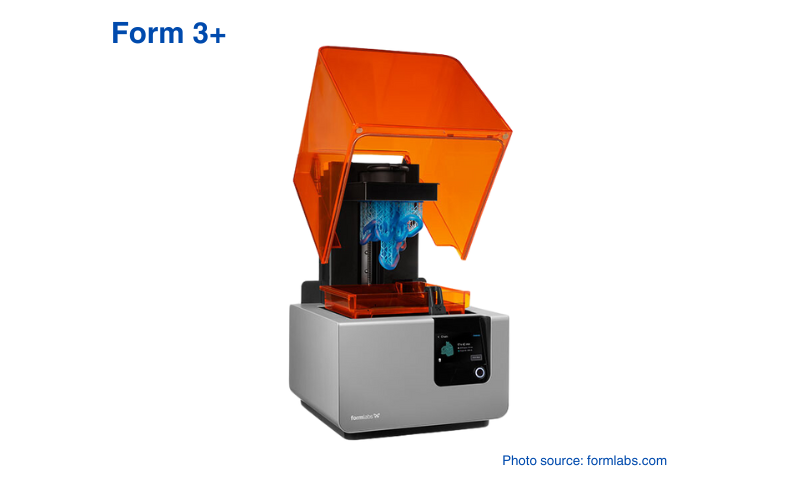
Key Features and Specifications
Key Features | Specifications |
---|---|
Pure Silicone Technology™ | Technology: Laser-Powered Stereolithography (SLA) |
Low Force Stereolithography (LFS) | Printer Engine: Low Force Stereolithography™ (LFS) |
Swappable Cartridge System | Build Volume: 145 × 145 × 185 mm |
5.5-inch Touchscreen Interface | Build Area: 210 cm² |
IModular, Easy-to-Maintain Design | Layer Thickness: 25 – 300 microns |
Spill-Free Material Management | Maximum Print Speed: 31 mm/hour |
PreForm, Dashboard, Fleet Control Software | Typical Print Speed² Average: 11 mm/hour across all materials Range: 4-17 mm/hour depending on the material |
Remote Print Monitoring via Dashboard | Material Compatibility: 27 Formlabs materials; or third-party materials using Open Platform |
Motorized Optics | Supports: Auto-generated, Light-touch removal |
TruTops Print Software for Easy Setup | Internal Temperature: Auto-heats to 35 °C (95 °F) |
Quick Cylinder Replacement | Operating Environment: 18–28 °C (64–82 °F) |
Force Sensing: Z-Axis Force Sensor: automatically optimizes print quality and print speed based on part geometry and selected material. | |
Connectivity Wi-FiPreForm, Dashboard, Fleet Control, Ethernet, USB-B 2.0 | |
The Formlabs Form has a build volume of 145 × 145 × 185 mm and a 5.5-inch touchscreen interface. The swappable cartridge system allows for quick material changes, while the spill-free material management system ensures a clean, efficient workflow. PreForm software enables intuitive part preparation. The printer also supports auto-generated, light-touch supports for easy removal and enhanced surface quality. The Form 3+ features motorized optics and force sensing, with a Z-axis force sensor. This optimizes print quality and speed based on part geometry and material selection. The printer maintains an internal temperature of 35 °C for optimal performance and operates best in environments ranging from 18–28 °C . It can print with 27 Formlabs materials and third-party options via the Open Platform. The Form 3+ can handle production for silicone and resin materials across various industries.
Comparisons
Form 3+ vs. Form 3
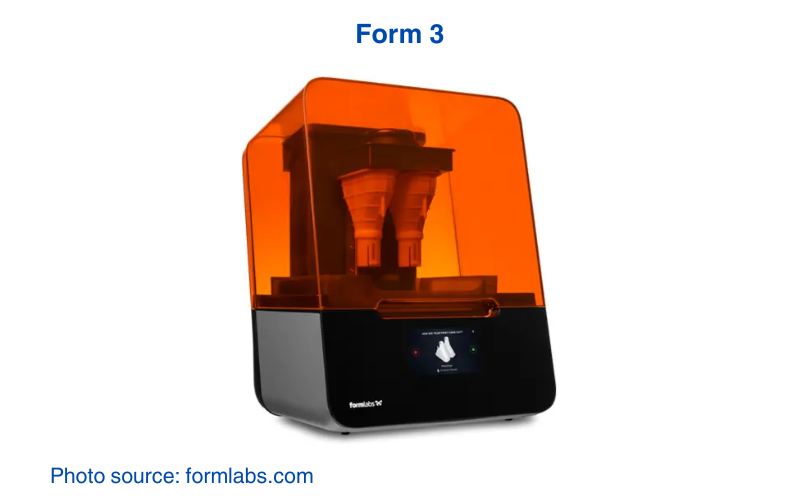
The Formlabs Form 3 and Form 3+ are both part of the same product line, designed for professional resin printing. However, the Form 3+ comes with several key upgrades over the Form 3.
Material Compatibility:
The Form 3+ introduces direct support for printing with the proprietary Silicone 40A Resin, making it a better option for industries that require flexible, durable silicone parts. The Form 3, while versatile with many resins, does not have this capability and is limited to more standard photopolymers.
Printing Speed:
One of the main improvements in the Form 3+ is faster print speeds. This is useful for larger, more complex prints or batch production jobs. The Form 3 has a slower throughput compared to the Form 3+, making the latter a more efficient option.
Design and Reliability:
Both models feature the same build volume and modular design. However, the Form 3+ offers enhanced reliability for long-term use. It reduces peel forces even further, thanks to its improved Low Force Stereolithography (LFS) system. This makes the Form 3+ better suited for consistently producing high-detail parts, especially when working with silicone.
Form 3+ vs. Form 4
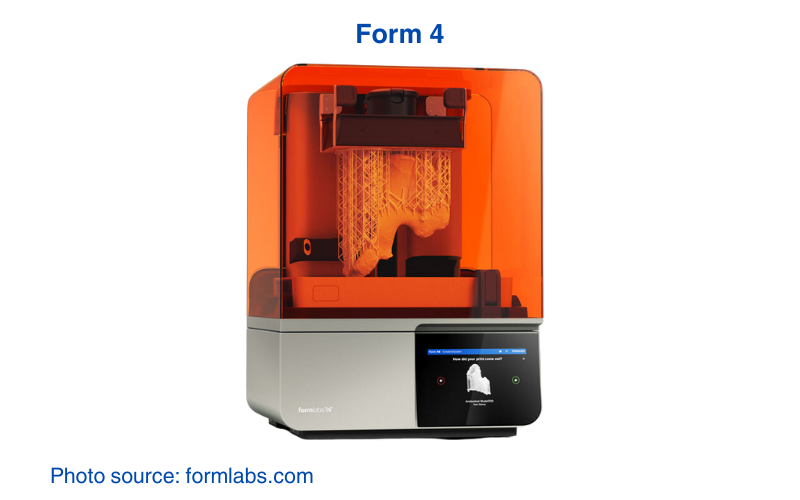
The Formlabs Form 4 is the next-generation model succeeding the Form 3+, with several improvements aimed at further enhancing speed, material compatibility, and overall performance.
Printing Speed:
The Form 4 has faster printing speeds compared to the Form 3+. While the Form 3+ is already optimized for speed with its LFS technology, the Form 4 refines the print process. This reduces layer times, and allows users to complete larger print jobs more efficiently. This makes the Form 4 a better choice for high-volume production environments.
Build Volume and System:
Both models share a similar build volume, but the Form 4 introduces improvements in overall stability and precision. The Form 4 features an upgraded mechanical system that further minimizes vibration and improves layer alignment.
Advanced Features:
While the Form 3+ is designed to be reliable and easy to maintain, the Form 4 offers new automation tools that further streamline the workflow. These tools are part of the Formlabs Automation Ecosystem, enabling 24/7 production with reduced manual intervention. The Form 4 is also more efficient when it comes to material management, offering faster and more intuitive material swaps.
Real World Applications
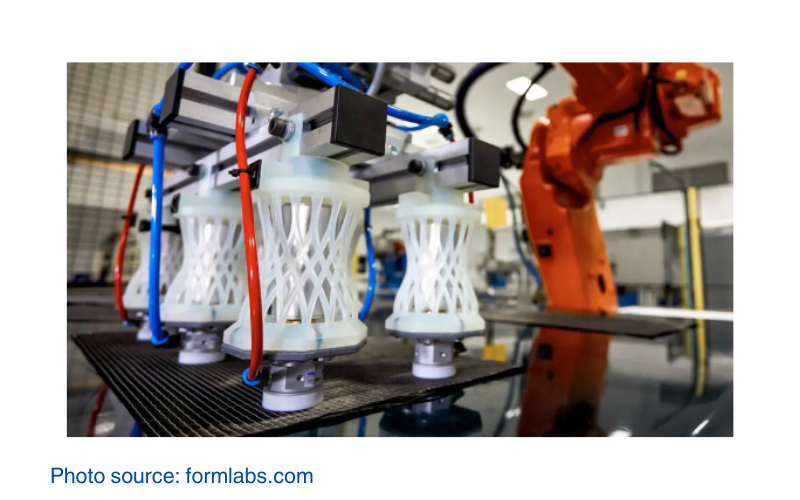
The Formlabs Form 3+ is highly adaptable and is useful across multiple industries. Here are some of the industries where the Form 3+ can be utilized:
Automotive & Transportation
In the automotive sector, the Form 3+ can be used to prototype components like gaskets, seals, and interior parts. Its precision allows for the creation of custom parts that are tested for fit and functionality before mass production. The printer is also used to create specialized tooling, such as jigs and fixtures, which streamline the manufacturing process.
Aerospace
The Form 3+ is valuable in aerospace for producing functional prototypes, such as aerodynamic components used in wind tunnel tests. Its ability to print intricate geometries makes it ideal for producing custom antenna prototypes and other components that require high accuracy. Additionally, the Form 3+ can be used to create lightweight, durable parts for aircraft interiors or equipment testing.
Manufacturing & Industrials
Manufacturers use the Form 3+ to create custom molds, replacement machine parts, and tooling used in production lines. The printer’s precision enables the rapid creation of jigs, fixtures, and other production aids that improve efficiency. Its ability to produce detailed, functional parts also allows for faster iterations of equipment and machinery designs.
Consumer Products
In the consumer goods industry, the Form 3+ is commonly used to create prototypes for product testing and design validation. Items such as custom phone accessories, wearable devices, and home products are developed using the printer to ensure the final design meets all requirements. Additionally, small-batch manufacturing of custom or personalized products can be achieved directly with the Form 3+.
Conclusion
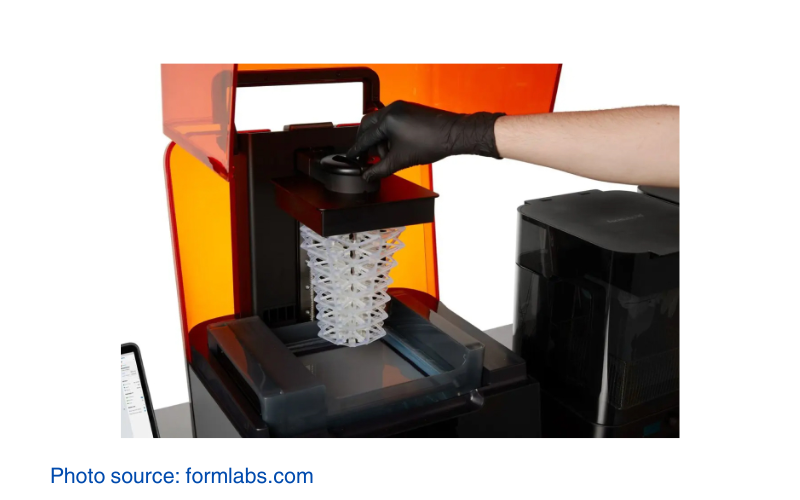
The Formlabs Form 3+ is an excellent choice for professionals and businesses who need a reliable resin 3D printer with the unique capability of directly printing with silicone. Professionals in product development, manufacturing, healthcare, or even prototyping industries can utilize the Form 3+ to create detailed, functional parts. Its support for over 45 materials, including the proprietary Silicone 40A Resin. The printer’s ease of use, modular design, and intuitive software successfully bridges the gap between high-end industrial printers and more accessible desktop models. Its ability to print directly with 100% silicone material is a game-changer for industries that need both accuracy and flexibility in their parts