Qidi Tech X-Max 3 Review
Large-format 3D printing opens up new possibilities by letting you print big, detailed projects in one piece rather than gluing smaller sections together. It’s a huge step forward for anyone who needs large parts—especially when durability matters.
3D printers come in all shapes and sizes, and the build volume is one of the biggest differences. Generally, 3D printers fall into a few size categories. Small printers, around 180 x 180 x 180 mm³, are great for hobby projects and small models. Standard-sized printers—closer to 250 x 250 x 250 mm³—are what most people start with. Mid-sized printers bump that up to 300 x 300 x 300 mm³, giving you a bit more room for larger ideas. A little above that and you step into large-format printers, about up to 400 x 400 x 400 mm³. This is ideal for bigger prototypes, cosplay parts, and functional pieces. Extra-large printers handle up to 500 x 500 x 500 mm³, and giant machines go beyond 600 x 600 x 600 mm³—some can even print over a meter tall in one job.
Companies like Qidi Tech have pushed the boundaries of what 3D printers can do. Their machines don’t just print larger—they also support advanced materials that need high temperatures and extra stability during the printing process. This makes large-format 3D printing practical for more than just industrial work. Today, engineers, designers, and independent creators can take on bigger projects without needing multiple machines or complicated setups.
In this review, we’re looking at the Qidi Tech X-Max 3. We’ll walk through its
Design and Build Quality
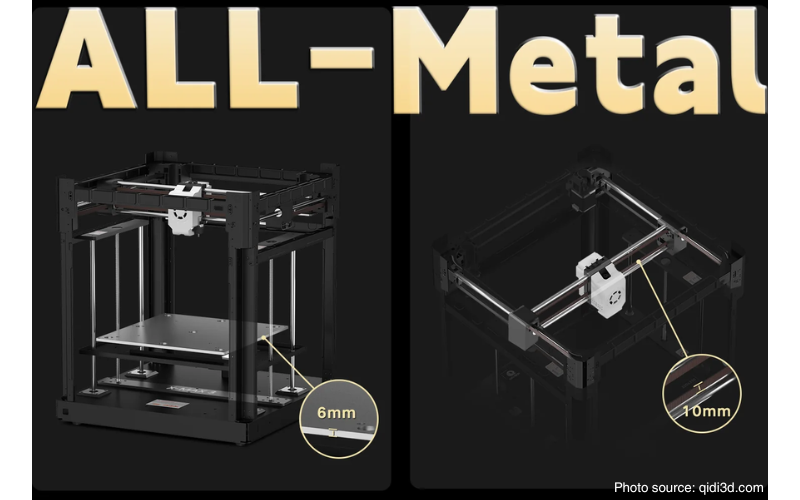
The X-Max 3 has a strong, all-metal enclosed frame that keeps things stable while printing. Its metal structure helps reduce vibrations, which can mess up large prints. The enclosed design helps keep the internal temperature consistent—a must when working with materials like ABS and nylon that tend to warp if the heat fluctuates too much.
Its 325 x 325 x 315 mm build volume gives you plenty of room for mid-to-large projects. It’s a great middle ground for those who need a bit more space without taking up too much room. The dual Z-axis system keeps taller prints steady, so you don’t end up with wobbly layers during long jobs.
The front door and side panels are transparent, so you can keep an eye on your prints without opening the enclosure and letting the heat escape. The build plate is magnetic and removable, making it easy to take out prints—especially useful for larger models that can stick to the plate. Setting up the X-Max 3 is straightforward. Most of it is already assembled when it arrives, so you won’t spend hours on complicated steps. Once it’s up and running, it operates quietly.
Key Features and Specifications
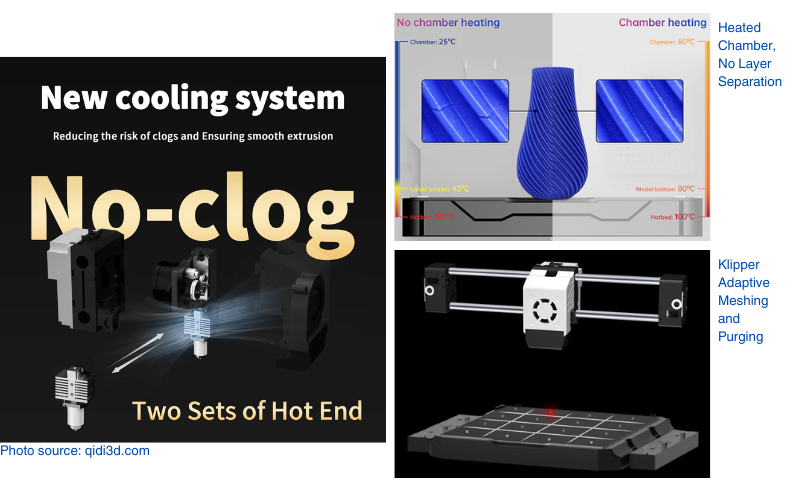
Key Features | Specifications |
---|---|
Large Build Volume | Build Volume: 325 x 325 x 315 mm³ |
Temperature Controlled Chamber And Drying Box | Printing Accuracy: ±0.1 mm |
Prints Professional Industrial-grade Materials | Maximum Extruder Temperature: 350°C |
Automatic Leveling: Klipper Adaptive Meshing and Purging | Printing Speed: ≤600mm/s |
Flexible HF Build Plate | Printing Acceleration:: 20000mm/s² |
High-Temperature Dual Extruder System | Extruder: High-flow Direct Drive Extruder |
5-inch Touch Panel | Extruder Flow: 35mm³/s |
Reliable Power-Loss Recovery | Chamber Temperature Control: ≤65°C |
Filament Detection | Nozzle diameter: Standard 0.4mm Optional: 0.2,0.6,0.8mm |
Resonance Compensation | Hotend (Included) For Common materials: Copper alloy nozzle hotend For Abrasive materials: Hardened steel nozzle hotend |
Connectivity: 150M 2.4G Wi-Fi, USB Flash Drive/Ethernet Cable | |
Recommended Filament: PAHT-CF,PET-CF,PA12-CF Compatible Filament: PLA, ABS, ASA, PETG, TPU, PC, UltraPA, Nylon, etc. |
Industrial-grade and High Speed? Count me in!
The X-Max 3 is built for large-scale, industrial-grade printing. It’s designed to handle tough jobs that need strong materials and bigger build sizes. One of its standout features is the dual extruder setup. It comes with a standard extruder for everyday filaments like PLA and PETG and a high-temperature extruder that can reach 350°C. This makes it great for printing advanced materials like carbon fiber-infused nylon and polycarbonate.
With a 325 x 325 x 315 mm build volume, there’s plenty of room for large prototypes, mechanical parts, or batch printing. The enclosed chamber keeps the temperature steady, cutting down the chances of warping when printing with ABS or similar materials. The heated bed reaches 120°C, giving the first layers a solid grip to avoid shifting during long prints.
For remote control and file transfers, the X-Max 3 supports Wi-Fi, USB, and Ethernet connections. You can send large files straight from your computer and check the print progress without standing next to the printer. The 4.3-inch touchscreen makes it easy to adjust settings and start jobs quickly.
Removing big prints is simpler thanks to the magnetic, removable build plate. Instead of struggling with a stuck print, you can pop off the plate, flex it, and lift the print off cleanly.
The printer also comes mostly pre-assembled, so you won’t spend hours setting it up. It’s ready to handle everything from durable prototypes to detailed models soon after unboxing.
Comparisons
Qidi Tech X-Max 3 vs Creality K1 Max
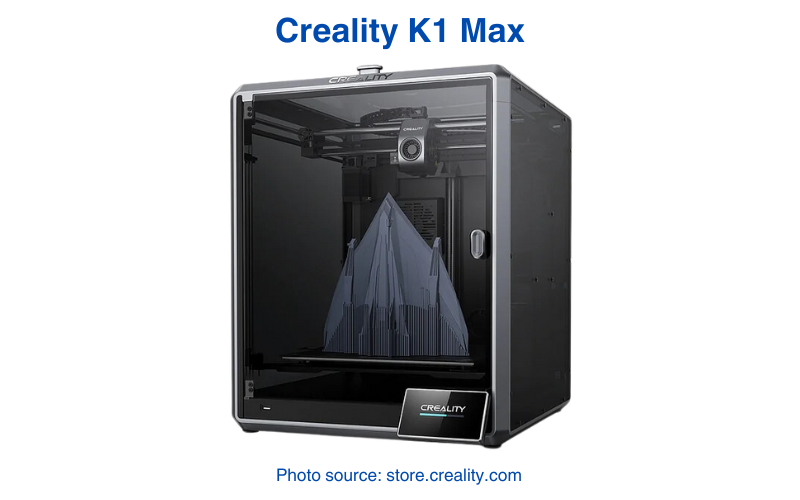
- Extruder System: The K1 Max has a single high-speed extruder for fast prints, but it doesn’t handle advanced filaments like polycarbonate or carbon fiber blends. The X-Max 3 has two extruders—one for standard materials and another that heats up to 350°C for tougher jobs.
- Build Volume: The K1 Max’s build volume is 300 x 300 x 300 mm, while the X-Max 3 gives you 325 x 325 x 315 mm. The extra height on the X-Max 3 makes it better for taller prints.
- Material Compatibility: The X-Max 3 supports a wider range of materials, thanks to its higher extruder temperature. The K1 Max is limited to lower-temp materials like PLA, PETG, and TPU.
- Connectivity: Both printers support Wi-Fi and USB, but the X-Max 3 also has Ethernet for a more stable, wired connection.
- Enclosure: The X-Max 3’s enclosed build chamber keeps temperatures steady. Which is more reliable for ABS and nylon. The K1 Max’s open design struggles with temperature-sensitive prints.
Qidi X-Max 3 vs Anycubic Kobra 3 Max Combo
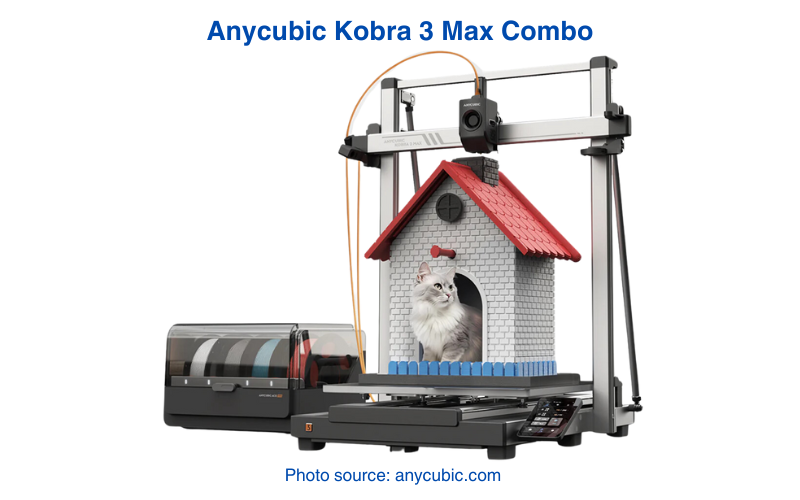
The X-Max 3 and Kobra Max 3 Combo both target users who want larger print sizes. But they differ when it comes to handling materials and overall design.
- Extruder System: The Kobra 3 Max Combo uses a single hardened steel extruder for basic filaments. Paired with the ACE Pro, it can also handle other advanced materials like ABS and ASA. The X-Max 3’s dual-extruder setup supports higher temps for more demanding materials.
- Build Volume: The Kobra 3 Max Combo has a bigger build volume at 400 x 400 x 450 mm that’s ideal for large projects. But the X-Max 3 focuses on material flexibility and can handle stronger, more technical prints.
- Temperature Capabilities: The X-Max 3’s extruder hits 350°C, while the Kobra Max can heat up to 300°C.
- Design: The X-Max 3 has an enclosed chamber that helps prevent warping with ABS and nylon. The Kobra Max’s open-frame setup works fine for PLA but struggles with anything more demanding.
Real World Applications
- Production-Ready End-Use Parts: Instead of just prototyping, the X-Max 3 can produce fully functional parts that are ready for use right off the print bed. This is especially useful for industries that need custom, large-scale components in low quantities. Examples are large machine housings, conveyor belt guides, and protective covers for industrial equipment. The enclosed design and dual extruder system make it possible to print complex shapes using materials like carbon-fiber nylon that are strong enough to replace metal in some cases.
- Batch Production of Oversized Components: When you need multiple large parts printed in one run, the X-Max 3’s spacious build volume makes it possible to print several at once. This is especially useful for manufacturing custom molds, large enclosures, or even sets of production fixtures. The high-temperature capabilities also mean that the printed parts can withstand demanding environments, making the X-Max 3 a valuable tool for industries like automotive and aerospace manufacturing.
- Large Custom Molds and Patterns: Creating large molds for casting metal, resin, or concrete is time-consuming and expensive with traditional methods. The X-Max 3 can print mold patterns for industrial casting that are strong, heat-resistant, and highly accurate. This is particularly valuable for foundries, where creating large patterns using traditional CNC machines can be costly and time-intensive. By printing patterns directly with heat-stable materials, you can skip several steps in the process.
- Full-Scale Industrial Prototypes: In industries like automotive and aerospace, creating full-scale prototypes can be difficult without large-format printers. The X-Max 3’s build size is large enough to print full sections of functional prototypes, such as dashboard panels, engine housings, or drone frames, all in one go. This not only saves time but also improves accuracy by avoiding seams or joints that can affect performance during testing.
- Large Structural Parts for R&D: Research and development labs often need to test custom, large-scale components like wind tunnel models, robotic arms, or load-bearing support structures. The X-Max 3’s ability to print tough materials like polycarbonate and carbon-fiber blends makes it a go-to machine for creating structural parts that mimic real-world use. Its large print area makes it possible to create these pieces without compromising their size or strength.
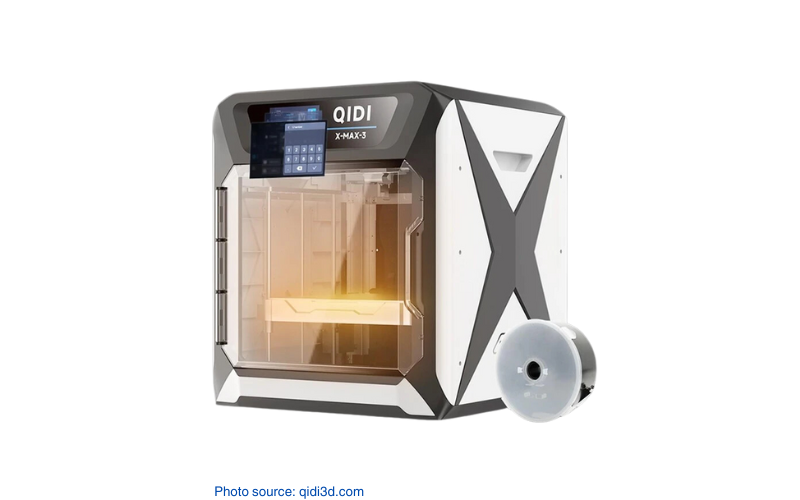
Final Notes
The Qidi Tech X-Max 3 is built for industrial projects that smaller 3D printers just can’t handle. With its 325 x 325 x 315 mm build volume, it can print large, single-piece parts without the need to split and reassemble. That’s a big deal for anyone working on large prototypes, molds, or production-ready components. The dual extruder setup—one of which heats up to 350°C—means you can work with advanced materials like carbon-fiber nylon and polycarbonate that most standard printers can’t touch.
The fully enclosed chamber keeps the temperature steady, so you’re less likely to run into warping or cracking when using tricky materials like ABS. The heated, magnetic build plate makes removing large, heavy prints easier without risking damage to the model or the bed.
Its connectivity options—Wi-Fi, USB, and Ethernet—make it flexible for different work environments. You can manage print jobs remotely or transfer large files directly from your computer. And since the printer comes mostly assembled, you won’t spend hours on setup—you’ll be up and printing quickly.
If you’re working on big, complex projects that need strong materials and a large print space, the X-Max 3 is built to handle it. It’s a great fit for anyone who needs industrial-grade parts without the limitations of smaller machines.