Markforged X7 Gen 2 Full Review
Markforged has carved out a name in 3D printing by transforming how industries think about manufacturing. In 2013, Greg Mark founded the company with the mission of making strong, functional parts more accessible. While most 3D printers have focused on plastics, Markforged took a bold step by using continuous fiber and metal. This led to the development of machines like the X7 Gen 2. It’s designed to deliver parts with the strength of metal but without the constraints of metalworking. It is made for professionals and for industrial use. Leveraging their proprietary Continuous Fiber Fabrication (CFF) technology, Markforged was able to create parts that are lightweight and incredibly strong—almost defying what you’d expect from a 3D printer. In this Markforged X7 Gen 2 full review, we will take a look at how this printer takes it a step further with even more precision, reliability, and capabilities.
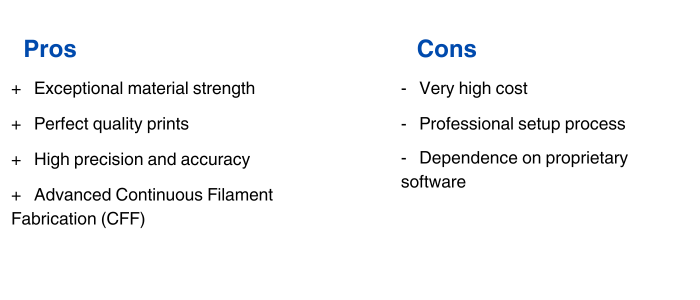
Design and Build Quality
Industrial-Grade Durability and Precision
The X7 Gen 2 showcases a design that speaks directly to its industrial capabilities. Encased in an aluminum frame, this 3D printer is built with the sturdiness for demanding environments. The exterior is sleek and minimalistic and features a fully enclosed build chamber. Which is important in maintaining a consistent internal temperature, essential for printing with materials like carbon fiber and Kevlar.
One of the standout features is its ultra-flat, precision-machined print bed. It is designed to reduce warping and ensure that each layer is laid down with pinpoint accuracy. This results in parts that are not only strong but also dimensionally accurate. This meets the stringent needs of industries such as aerospace and automotive. The X7 Gen 2 also includes an integrated laser micrometer that automatically calibrates the print bed before each job. It further enhances its ability to produce consistently high-quality prints.
Professional Setup
As expected from an industrial-grade machine, the setup process is more involved than that of typical desktop 3D printers. This isn’t a plug-and-play device. Instead, it is a little more complex to make sure that every component is correctly aligned and calibrated. The printer arrives mostly pre-assembled. The final setup involves precise calibration, connection of the external filament holder, and proper alignment of the print bed and laser micrometer.
Users should anticipate dedicating a couple of hours to getting the X7 Gen 2 ready for its first print. This includes installing the Eiger software, Markforged’s cloud-based platform. The setup process may be more complex, but it reflects the X7 Gen 2’s professional-grade capabilities and the high standards it is designed to meet. Once the printer is fully calibrated and configured, it integrates smoothly into a production environment, where it can consistently deliver high-strength, precision parts.
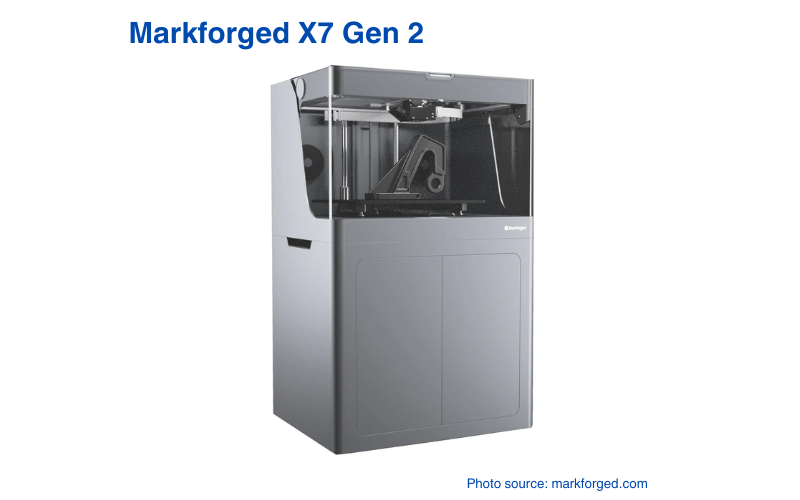
Key Features and Specifications
Key Features | Specifications |
---|---|
Dual Nozzle Print System | Build Volume: 330 x 270 x 200 mm (13 x 10.6 x 7.9 in) |
Laser Inspection System | Machine Footprint: 584 x 483 x 914 mm (23 x 19 x 36 in) |
Continuous Filament Fabrication (CFF) | Weight: 48 kg (106 lbs) |
Precision-Machined Gantry and Print Bed | Layer Height: 100 μm default, 50 μm minimum, 250 μm maximum |
Out-of-Plastic and Out-of-Fiber Detection | Nozzle Diameter: 0.4 mm |
Integrated Laser Micrometer | Max Nozzle Temperature: 300°C |
Automatic Material and Fiber Detection | Power: 100–240 VAC, 150 W (2 A peak) |
Kinematic Coupling Print Bed | RF Module: 2.4 GHz Wi-Fi, Standards 802.11 b/g/n |
Blacksmith Adaptive Manufacturing Platform | Tensile Strength: 800 MPa (25.8x ABS, 2.6x 6061-T6 Aluminum) |
Reinforced Print System | Tensile Modulus: 60 GPa (26.9x ABS, 0.87x 6061-T6 Aluminum) |
Filament Compatibility: Onyx, Onyx FR, Onyx ESD, Nylon White, P-PLA, S-TPU | |
Fiber Compatibility: Carbon Fiber, Carbon Fiber FR, Fiberglass, Aramid Fiber (Kevlar®), HSHT Fiberglass |
The X7 Gen features a dual nozzle print system and Continuous Filament Fabrication (CFF). This allows for the creation of high-strength composite parts. The integrated laser micrometer and precision-machined gantry ensure that every print meets strict dimensional tolerances. It has advanced features like out-of-material detection and cloud-connected Eiger software. This makes the X7 Gen 2 ideal for reliable, high-performance 3D printing in professional environments. The printer’s strong build and its ability to handle a wide range of materials, makes it a powerful tool for industrial applications.
Comparison
X7 Gen 2 vs. X5
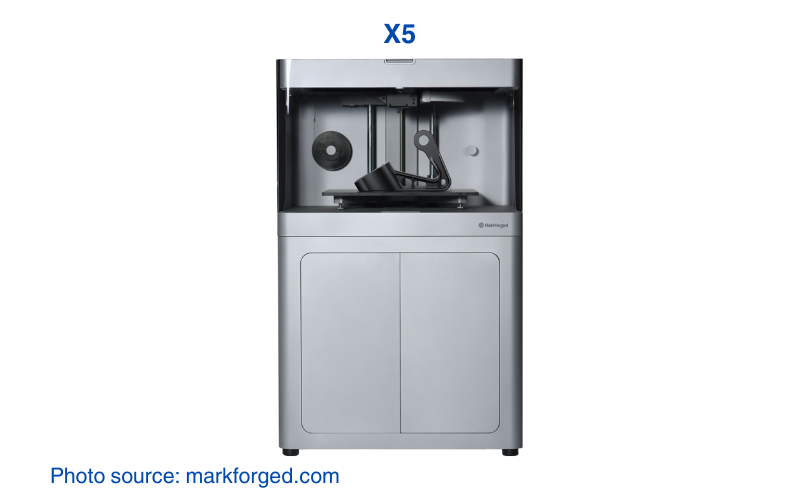
When comparing the X7 Gen 2 with its sibling, the X5, several key differences could influence your decision to purchase:
Build Volume: Both the X7 Gen 2 and the X5 share the same build volume of 330 x 270 x 200 mm. This build is ample for industrial-grade parts. However, the X7 Gen 2 enhances the printing process with more advanced laser inspection and calibration features.
Material Compatibility: The X5 supports the same high-performance materials as the X7 Gen 2, including Onyx, Carbon Fiber, and Kevlar®. However, the X7 Gen 2’s Continuous Filament Fabrication (CFF) capabilities are more refined for greater precision and consistency in fiber reinforcement.
Inspection System: The X5 includes basic laser inspection, which ensures dimensional accuracy during printing. The X7 Gen 2, however, takes this a step further with an integrated laser micrometer that scans the print bed with 1 μm accuracy. This ensures optimal bed adhesion and part accuracy right from the first layer.
X7 Gen 2 vs. X3
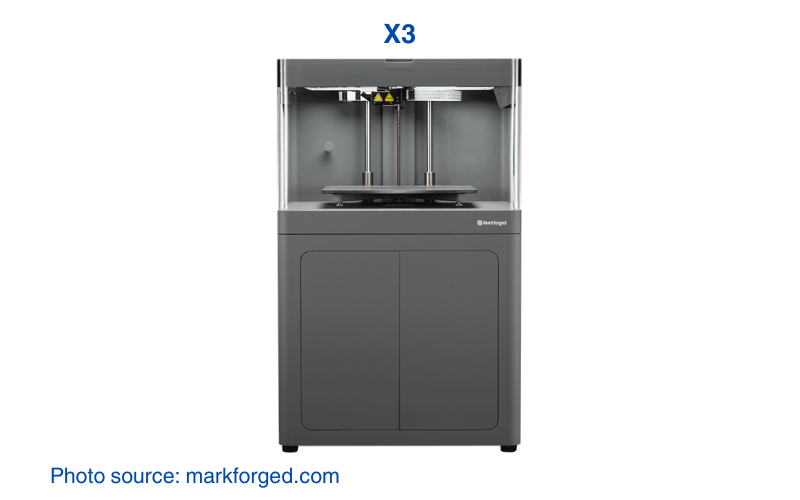
Another important comparison is between the X7 Gen 2 and the entry-level X3. This one can be used by professionals who need strong, functional parts,too. But Markforged has created more capabilities that are now in X7 Gen 2 :
Build Volume: The X3 shares the same build volume as the X7 Gen 2, at 330 x 270 x 200 mm, making it a capable machine for various applications. The primary difference lies in the range of materials and the advanced features offered by the X7 Gen 2.
Material Compatibility: The X3 focuses on Markforged’s proprietary Onyx material but lacks the ability to print with continuous fibers like Carbon Fiber or Kevlar®, which are key features of the X7 Gen 2.
Advanced Features: The X7 Gen 2’s laser inspection system, automatic material and fiber detection, and dual nozzle print system give it a significant edge in producing high-strength, precise parts. These features are absent in the X3, making the X7 Gen 2 the better choice for more demanding applications where material strength and precision are paramount.
Price: The X3 is more budget-friendly, making it an excellent entry point into Markforged’s ecosystem. The X7 Gen 2, while more expensive, justifies its higher price with advanced capabilities, offering greater versatility and precision for those who require top-tier performance.
Real World Applications
The X7 Gen 2 is specifically designed for industrial use. It’s where precision, strength, and the ability to handle advanced materials are non-negotiable. Here’s a closer look at how various industries leverage this powerful machine:
Aerospace Component Production
In the aerospace sector, the X7 Gen 2 can be used in producing parts that need to be both incredibly strong and lightweight—two critical factors for flight. Engineers can use this printer to manufacture complex components such as turbine blades, structural brackets, and custom tooling. The Continuous Filament Fabrication (CFF) technology allows for the integration of carbon fiber. It gives these parts the necessary rigidity and durability while keeping the weight to a minimum.
Automotive Prototyping and Production Tools
In automotive manufacturing, the X7 Gen 2 can excel at producing end-use parts and highly durable tooling that can withstand the demands of production environments. It can be utilized to create custom jigs, fixtures, and assembly tools for specific vehicles or manufacturing processes. For example, a car manufacturer might use the X7 Gen 2 to produce carbon fiber-reinforced fixtures that hold components in place during assembly. The printer’s ability to produce parts with high tensile strength and resistance to wear makes it ideal for creating tools that need to last through repeated use in a busy manufacturing setting.
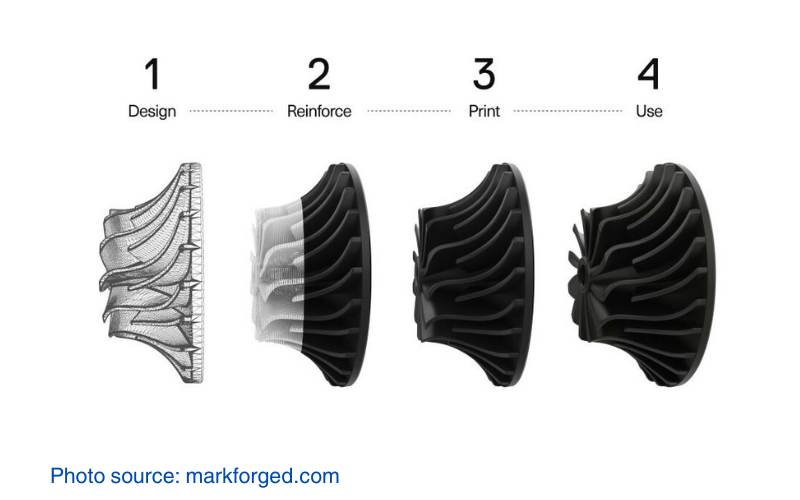
Defense and Military Equipment
In the defense industry, where reliability and strength are most important, the X7 Gen 2 can be used to produce mission-critical components. For instance, the printer can be used to manufacture lightweight armor panels and protective housings that integrate Kevlar® reinforcement. The ability to produce durable parts that can withstand harsh environments and intense operational conditions is a key advantage, as these parts need to perform consistently under stress.
Oil and Gas Industry Tooling
The oil and gas sector requires tools and components that can endure extreme conditions. Environments that have high pressures, temperatures, and corrosiveness. The X7 Gen2 can be utilized to create custom tools like pipe clamps, drill guides, and sensor housings. These need to be reinforced with materials like HSHT Fiberglass (High Strength High Temperature) to withstand these harsh environments. The precision and material strength given by the X7 Gen2 make it possible to produce parts that can be deployed directly into the field.
Conclusion
The Markforged X7 Gen 2 stands at the intersection of tradition and innovation, challenging the norms of manufacturing with a bold approach that goes beyond conventional 3D printing. It empowers engineers to design with materials that have the strength of metal but the flexibility and weight of composites. This enables the creation of parts that aren’t just replacements for traditional components but enhancements, too. For aerospace, it’s about reducing weight without compromising integrity. In automotive, it’s about pushing the limits of what custom tooling can achieve. In defense and medical fields, it’s creating solutions that are as resilient as they are innovative.
The X7 Gen2 is a machine that challenges industries to rethink tomorrow. It’s about more than keeping pace with technological advancement; it’s about setting the pace. By combining precision, material science, and intelligent software, the X7 Gen2 opens the door to more and more possibilities.