MakerBot Method X Full Review
Since its inception in 2009, MakerBot has made innovations for desktop 3D printing. Now operating under the leadership of Stratasys, MakerBot continues to deliver high-performance solutions for professionals who need reliable and advanced FDM 3D printers. The Method series are professional-grade 3D printers consisting of the original Method, Method X, Method Carbon Fiber and Method XL. This line is made for commercial and educational use, with features and capabilities to print high-performance filaments . In this Makerbot Method X full review, we will take a look at the features and capabilities of this 3D printer. Specifically its advanced version designed specifically to handle carbon fiber 3D printing and other high-performance materials.
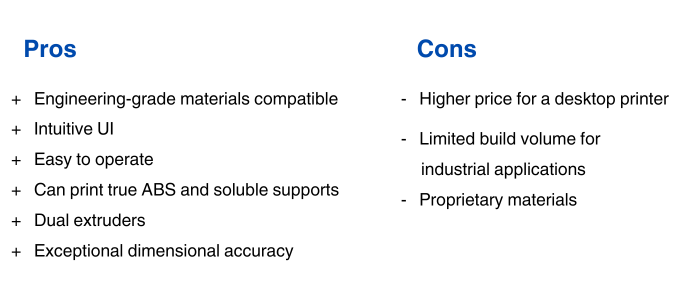
Design and Build Quality
Built for Professional Use
The MakerBot Method X is crafted for professionals, emphasizing both durability and precision. The printer features a metal frame that runs the length of its body, significantly reducing flexing during operation. This results in more consistent prints with improved accuracy and fewer failures. The fully enclosed build chamber is not just about safety; it also helps maintain a controlled environment.
With a heated build chamber capable of reaching temperatures up to 110°C, the Method X ensures that materials like ABS, PC-ABS, and ASA adhere properly and cool evenly. The printer’s rigid structure and advanced thermal regulation system makes it a reliable choice for 3D printing strong parts for functional prototyping or end-use production.
Available in Two Variations
The Method X has two configurations: the standard Method X and the Method X Carbon Fiber. The standard version comes equipped with the 1XA and 2XA extruders, which prints materials including ABS, ABS-R, PC-ABS, and ASA. This configuration is ideal for users focused on creating durable prototypes and parts with traditional engineering plastics.
On the other hand, the Method X Carbon Fiber model steps up the game by including the 1C extruder, specifically designed to handle abrasive materials. This can print advanced composites like Nylon Carbon Fiber, Nylon 12 Carbon Fiber, and the newly introduced ABS Carbon Fiber, expanding the printer’s capabilities to produce even stronger, lighter parts.
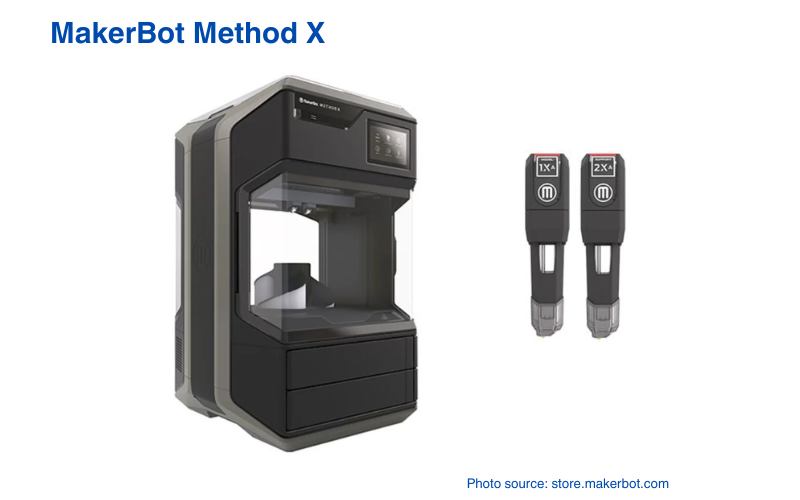
Key Features and Specifications
Key Features | Specifications |
---|---|
Dual Extrusion System | Build Volume (Dual Material): 152 x 190 x 196 mm |
5-inch Capacitive Touchscreen Interface | Build Volume (Single Material): 190 x 190 x 196 mm |
Heated Build Chamber | Heated Chamber Max Temperature: 110°C |
VECT™ 110 Thermal Regulation System | Print Speed: Up to 100 mm/s |
SmartAssist Material Loading | Layer Resolution: 20-400 microns |
RapidRinse™ Soluble Supports | Nozzle Diameter: 0.4 mm |
CloudPrint™ Remote Access | Maximum Bed Temperature: 120°C |
Direct Drive Extruders | Maximum Extruder Temperature: 300°C |
Auto-Calibration | Extruder Type: Swappable Performance Extruders |
Compatible with UltiMaker Cura | Compatible Filament Diameter: 1.75 mm |
Dry-Sealed Material Bays | Filament Compatibility: ABS, ABS-R, Nylon, Carbon Fiber, PC-ABS, ASA, PETG, PLA |
The Method X and Method X Carbon Fiber are equipped with a Dual Extrusion System for complex prints. Both have a build volume of 190 x 190 x 196 mm and a heated build chamber reaching up to 110°C. The 5-inch capacitive touchscreen interface provides an intuitive user experience, allowing for easy setup and real-time control. Method X supports a wide range of filaments, including ABS, ABS-R, Nylon, Carbon Fiber, PC-ABS, ASA, and PETG, enabling high-quality prints with layer resolutions ranging from 20 to 400 microns.
Both models feature a rigid metal frame that minimizes flexing, ensuring stable and accurate prints, even during long runs. The VECT™ 110 Thermal Regulation System maintains a controlled print environment, leading to stronger and more accurate parts, especially on the z-axis. With CloudPrint™ remote access, users can manage and monitor their prints from anywhere. Additionally, the flexible and removable build plate simplifies post-processing, while the SmartAssist Material Loading system makes material changes quick and hassle-free.
Comparisons
Method vs. Method X
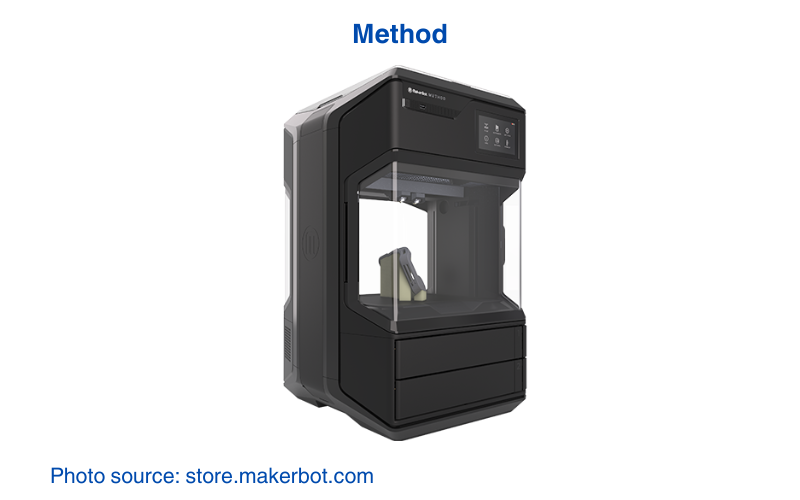
Comparing the original Method to the Method X, both printers are designed for professional use. But the Method X offers significant upgrades that enhance its capabilities:
Extruder System: The original Method comes with a standard dual extrusion system, which is well-suited for general-purpose printing. The Method X, on the other hand, includes the 1XA and 2XA extruders. These are specifically engineered to handle materials like ABS, PC-ABS, and ASA. This makes the Method X a better option for those needing to print with engineering-grade materials.
Heated Build Chamber: The Method features a partially heated build chamber that helps reduce warping in certain materials. However, the Method X takes this further with a fully heated chamber capable of reaching 110°C. This allows for better layer adhesion and dimensional accuracy, especially when printing with materials like ABS that require higher temperatures.
Material Compatibility: Method is compatible with a variety of materials, including PLA, PETG, and Nylon. The Method X expands this compatibility to include high-performance materials like ABS-R and new soluble support materials. This broadens the range of applications for the Method X, making it more versatile for industrial prototyping and production.
Method X vs. Method XL
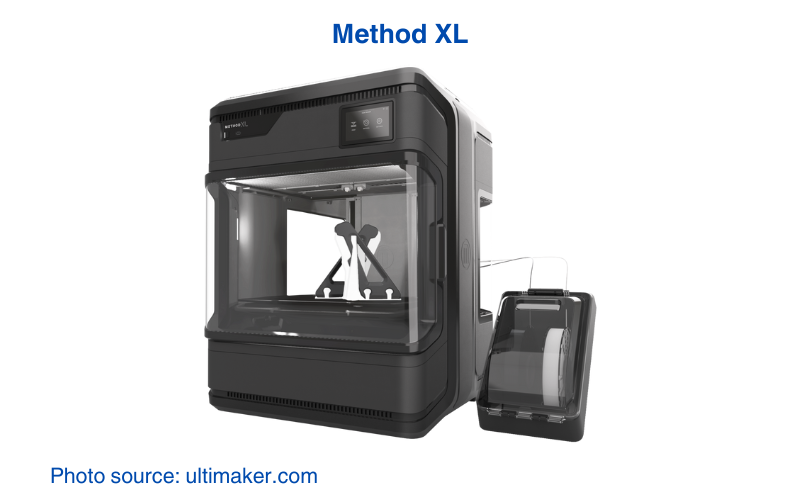
When comparing the Method X to the Method XL, both printers are top-tier options in the MakerBot lineup, but they serve different needs:
Build Volume: The Method X has a build volume of 190 x 190 x 196 mm. The Method XL, however, has a significantly larger build volume of 305 x 305 x 320. Which makes it better for producing bigger parts or multiple components in a single print job.
Extruder Options: The Method X comes equipped with performance extruders like the 1XA and 2XA. The Method XL expands on this by offering additional extruder options, including the LABS GEN 2 Experimental Extruder, which allows for the use of third-party materials. This feature makes the Method XL more versatile for experimental and custom applications.
Application Focus: The Method X is made for high precision and strong prints. Particularly for working with challenging materials like ABS and carbon fiber composites. The Method XL, while also capable of handling these materials, is better suited for projects that require a larger build volume and the flexibility to experiment with different materials. This makes the Method XL a better choice for industrial users who need both size and material versatility.
Real World Applications
The MakerBot Method X is known for its ability to print with carbon fiber-reinforced materials. This 3D printer is particularly well-suited for industries that require high-performance parts with lightweight characteristics. Below are some examples of how the Method X Carbon Fiber can be utilized in various advanced fields:
Aerospace Engineering
In the aerospace industry, reducing weight without compromising strength is essential for improving fuel efficiency and overall performance. The Method X Carbon Fiber allows aerospace engineers to create lightweight components using carbon fiber composites, which are known for their high strength-to-weight ratio. For instance, companies can use the Method X Carbon Fiber to produce custom brackets and supports for aircraft interiors. These components can be subjected to rigorous stress testing, including simulated flight conditions, to ensure they meet industry standards for durability and performance. The ability to print these parts in-house accelerates the prototyping process and reduces lead times.
Automotive Manufacturing
The automotive industry increasingly relies on 3D printing for both prototyping and producing functional parts. The Method X Carbon Fiber enables manufacturers to produce components that lightweight and strong enough to withstand automotive applications. For example, automotive companies can print custom engine mounts or structural brackets that must endure high mechanical loads. These carbon fiber parts can be tested in real-world conditions. Such as high-vibration environments or extreme temperatures, ensuring that they perform reliably in the final vehicle assembly.
Industrial Tooling and Fixtures
In manufacturing, custom tooling and fixtures are essential for efficient production processes. The Method X Carbon Fiber enables the creation of durable and precise tools that can withstand repeated use in harsh industrial environments. For example, a manufacturing company might use the Method X Carbon Fiber to print custom jigs or fixtures that are used in the assembly line. These carbon fiber tools can be designed to be lightweight yet strong enough to handle heavy-duty tasks. The ability to produce these tools quickly and in-house can significantly reduce downtime and improve production efficiency.
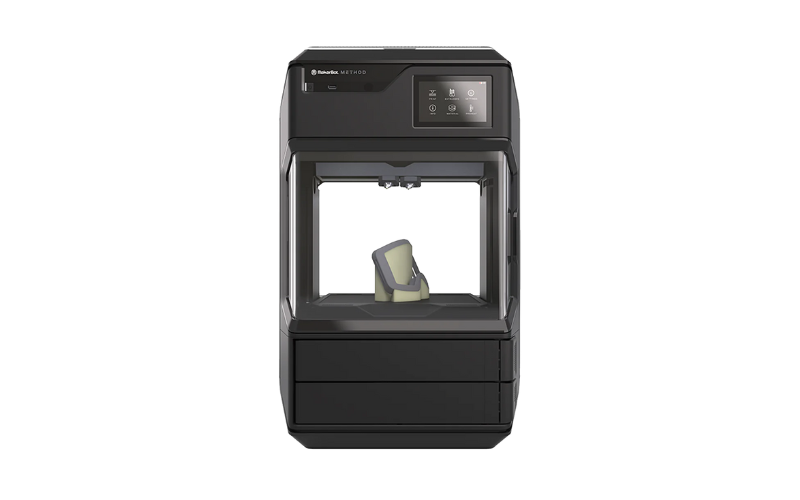
Conclusion
The MakerBot Method X is a powerful tool for professionals who need to produce strong, lightweight, and precise parts. Its ability to handle engineering-grade filaments such as carbon fiber for 3D printing, makes it an excellent choice for industries like aerospace, automotive, and industrial tooling. With advanced features like the heated build chamber, VECT™ 110 Thermal Regulation, and the versatile extruder system, this printer has the reliability and performance needed for demanding applications. In prototyping or producing functional parts, the Method X Carbon Fiber delivers the quality and efficiency that modern industries require.
Comments are closed.