Prusa XL Review
Large-format 3D printing opens up a whole new world of possibilities that smaller desktop printers just can’t match. Standard 3D printers work well for smaller parts and everyday projects. But when you need to create big, single-piece prints, that’s where large-format machines come in. Instead of printing separate sections and gluing them together, you can print an entire piece at once. It saves time and avoids weak points where seams would normally be.
When it comes to build sizes, printers generally fall into a few groups. Small printers handle around 180 x 180 x 180 mm³, standard ones cover about 250 x 250 x 250 mm³, and mid-sized machines go up to 300 x 300 x 300 mm³. Large-format printers push things further with 400 x 400 x 400 mm³, while extra-large machines can handle up to 500 x 500 x 500 mm³. Then there are the true giants, capable of printing over 600 x 600 x 600 mm³—or even larger.
This kind of scale is a game-changer for industries like automotive, architecture, and even artists working on large installations. Instead of assembling multiple pieces, professionals can print parts that fit together perfectly or even print single objects like furniture or life-sized sculptures. But there’s a tradeoff—large-format printers need more space, more power, and more upkeep. They’re built to handle long print jobs and heavier workloads.
Prusa, already well-known in the 3D printing space, took a big leap into this category with the Prusa XL. In this review, we’re taking a closer look at what the Prusa XL brings to the table and how it performs when tackling large-format printing projects.
Design and Build Quality
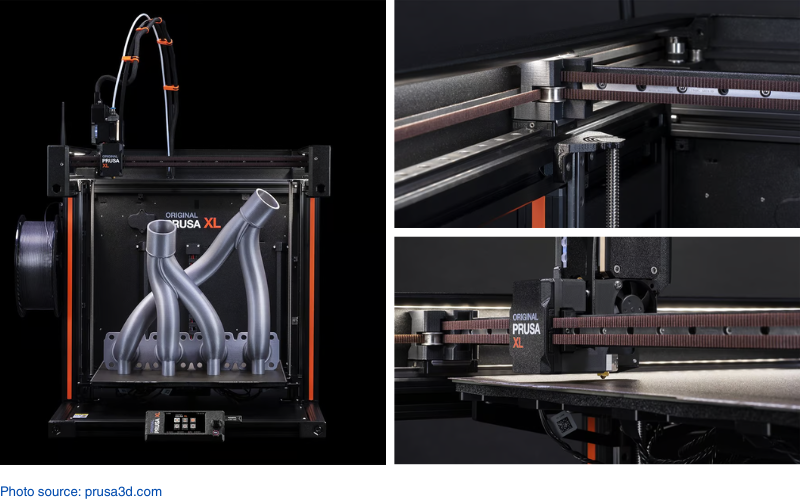
The Prusa XL is built to handle large-format 3D printing without feeling over-engineered or clunky. Its sturdy aluminum frame keeps everything stable during big print jobs, which is key when working with larger models. The open-frame design makes it easy to access different parts of the machine, while the reinforced build helps cut down on vibrations that could mess with print quality.
One of the first things you notice is its sheer size. But that bigger footprint means you can print larger projects in one go instead of splitting them into sections. Prusa also designed the frame to be modular, so swapping out parts or upgrading down the line is pretty straightforward.
The segmented print bed is unique. Instead of heating the whole thing all at once, it heats in sections, which keeps it more energy-efficient and helps prevent the dreaded bed warping that can happen with larger machines. The triple Z-axis setup keeps everything aligned and smooth, even when the extruder is moving across the entire build plate.
In short, the Prusa XL’s design feels solid and practical, making it a good fit for anyone who wants to print big projects without constantly fiddling with maintenance or stability issues.
Key Features and Specifications
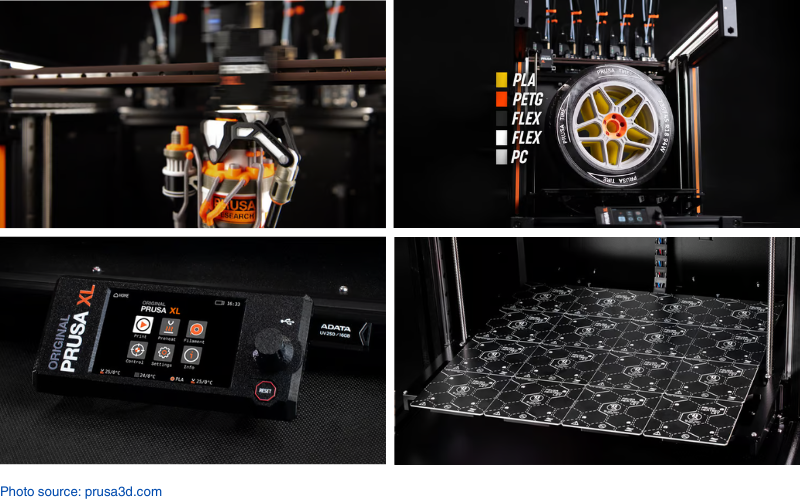
Key Features | Specifications |
---|---|
Modular Toolchanger with Up to 5 Heads | Build Volume: 360 x 360 x 360 mm³ |
Advanced Calibration and First-Layer Accuracy | Layer Height: 0.05 – 0.30 mm |
Zero-Waste Multi-Material Printing | Nozzle: 0.4 mm (interchangeable), max temperature 290°C / 554°F |
Segmented Heated Bed | Extruder Type: Nextruder, direct drive, E3D V6 compatible |
Nextruder with Precision Control | Filament Diameter: 1.75 mm |
Fast and Quiet Printing | Supported Materials: PLA, PETG, Flex, PVA, PC, PP, CPE, PVB, ABS, ASA, HIPS, and more |
Massive Printing Capacity with Spool Join | Maximum Flow Rate: 32 mm³/s (with Phrozen High-SHeated Bed: Segmented with 16 individually controlled tiles, max temperature 120°C / 248°F |
Reliable Power-Loss Recovery | Connectivity: USB, LAN, Prusa Connect (Wi-Fi option included) |
XL means Big Capabilities
The Original Prusa XL is built for large-scale projects, with a tool-changing system that can hold up to five toolheads. This lets you print with multiple colors or materials without waiting for filament swaps. Its segmented heatbed only heats the sections you needo tkeep temperatures even across the surface. The direct-drive Nextruder, with its 10:1 planetary gearbox, handles everything from flexible filaments to tricky overhangs without missing a beat.
Instead of using bulky purge blocks, the XL uses wipe-to-infill options to cut down on filament waste and keep costs low. With Input Shaper and Pressure Advance, you get fast prints without sacrificing quality. The Phase Stepping tech keeps the machine surprisingly quiet, even during long jobs. The loadcell sensor makes sure every first layer goes down perfectly—no manual tweaks needed. If you’re working on massive prints, the Spool Join feature switches spools automatically so you can print up to 10 kg without stopping. The XL also comes with wired and wireless connectivity for easy remote control, plus offline options if you prefer local control. And if the power goes out, the printer picks up right where it left off once it’s back on. All of these features make the Prusa XL a solid choice for anyone tackling large, multi-material projects.
Comparisons
Prusa XL vs Qidi X-Max 3
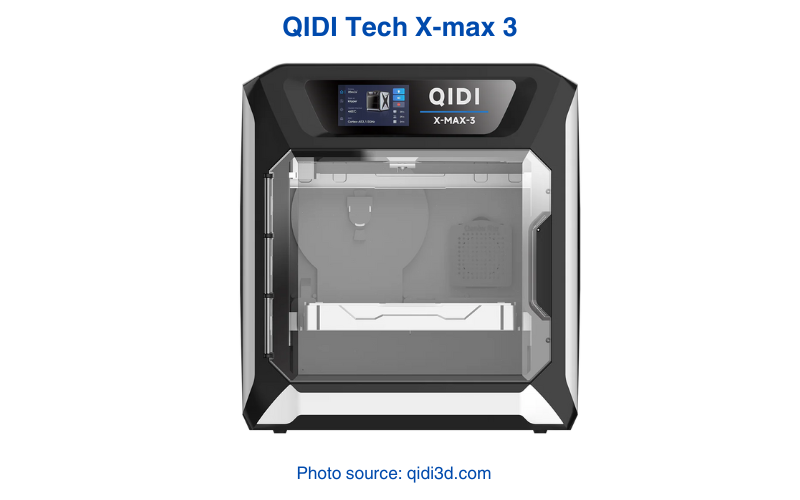
The Prusa XL and Qidi Tech X-Max 3 are both designed for ambitious projects, but are made for different types of users. The Qidi Tech X-Max 3 excels at handling tough, industrial-grade materials. While the Prusa XL is exceptional for its multi-material capabilities and advanced automation.
- Extruder System: The X-Max 3 comes with two swappable extruders—one for standard materials and another that can handle temperatures up to 350°C for advanced filaments like nylon and polycarbonate. The Prusa XL, on the other hand, uses a modular toolchanger with up to five direct-drive toolheads. This enables seamless multi-material and multi-color printing without purging waste blocks.
- Build Volume: The X-Max 3 has a build volume of 325 x 325 x 315 mm³. While the Prusa XL has a slightly larger 360 x 360 x 360 mm³ space. This provides more room for bulkier prints.
- Material Compatibility: Both printers support different printing materials. But the X-Max 3’s high-temp extruder is better for industrial-grade filaments like carbon-fiber-filled nylon. The Prusa XL also handles technical filaments but is more flexible with multi-material prints and wipe-to-infill options to minimize waste.
- Enclosure: The X-Max 3 features a fully enclosed build chamber, which helps maintain a stable print environment for temperature-sensitive materials. The Prusa XL has an open-frame design by default. But you can add an enclosure for materials like ABS and ASA if needed.
- Ease of Use: The Prusa XL’s automatic calibration, loadcell-based first-layer adjustment, and Spool Join feature make it more beginner-friendly for large and complex prints. The X-Max 3 has manual and semi-automatic calibration but may require more fine-tuning when working with higher-temperature filaments.
Prusa XL vs Elegoo Neptune 4 Max
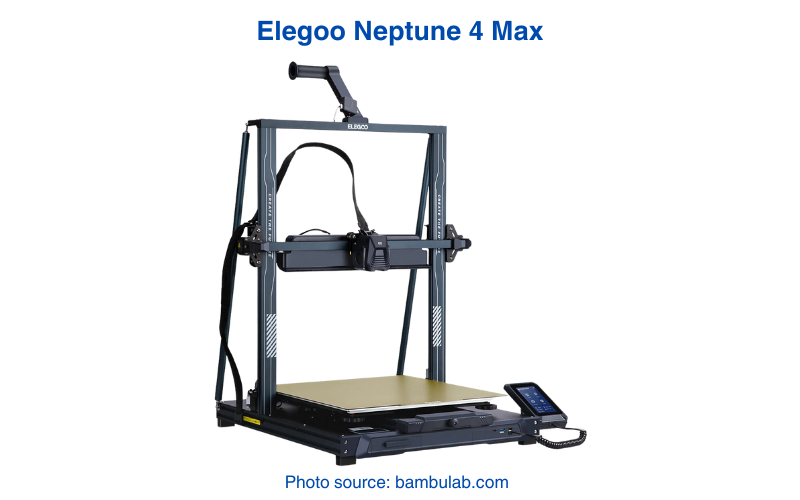
The Prusa XL and Elegoo Neptune 4 Max both cater to users who want large print sizes, but they differ in terms of versatility and overall features. The Neptune 4 Max focuses on high-speed, single-material printing, while the Prusa XL shines in multi-material, precision printing.
- Extruder System: The Neptune 4 Max features a single high-speed direct-drive extruder that supports standard filaments like PLA and TPU. The Prusa XL’s multi-toolhead system supports up to five toolheads. It’s capable of printing with multiple colors or materials in the same project.
- Speed: The Neptune 4 Max is designed for fast printing with speeds up to 500 mm/s, though faster speeds may affect print quality. The Prusa XL balances speed with quality using Input Shaper and Pressure Advance, reducing artifacts at higher speeds without sacrificing precision.
- Heated Bed: The Neptune 4 Max uses a standard single-zone heated bed, which can take longer to heat and may have slight inconsistencies in large prints. The Prusa XL’s segmented heatbed only heats the areas needed for the print, cutting down on power consumption and improving heat distribution.
Real World Applications
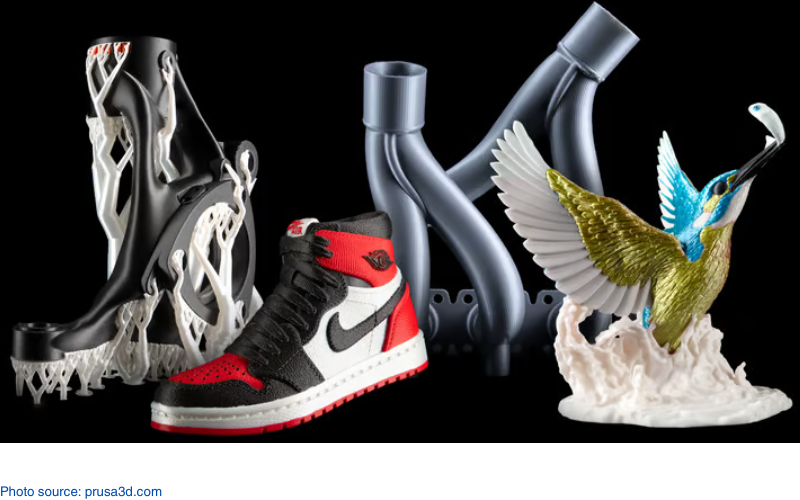
The Prusa XL’s features make it perfect for projects that push the limits of what typical 3D printers can handle. Here are some creative ways it can be put to use:
- Full-Scale Construction and Architectural Details: The XL can print complex building details, like facade sections or interior designs, in one go, and even using different materials. Need flexible seals or rigid support in the same part? No problem—the XL handles it all in a single job.
- Medical Devices and Prosthetics: When it comes to custom prosthetics or orthotic braces, precision and multiple materials are key. The Prusa XL can print flexible sections alongside rigid frames, making it easier to produce patient-specific parts without extra assembly. Its large print area means you can print full-sized prosthetic limbs or detailed surgical training models in fewer pieces.
- Large-Scale Casting Molds: If you’re working with resin or metal casting, the XL’s massive build area is perfect for printing large molds or master patterns. The segmented heated bed helps keep these big prints stable and warp-free, while the wipe-to-infill feature reduces wasted material during setup.
- Robotics Parts with Mixed Materials: Robotic parts often need a mix of flexibility and strength—like a rigid body with soft joints or dampeners. The XL’s toolchanger lets you load different materials and print everything in one go. This makes it easier to create parts like custom gears, casings, and flexible mounts without needing to assemble multiple pieces.
- Custom Lab Equipment: Research labs can use the XL to print experimental tools like fluidic devices or sample holders with built-in seals and channels. The XL’s support for high-temperature, chemical-resistant materials means you can print parts that hold up under extreme lab conditions.
Final Notes
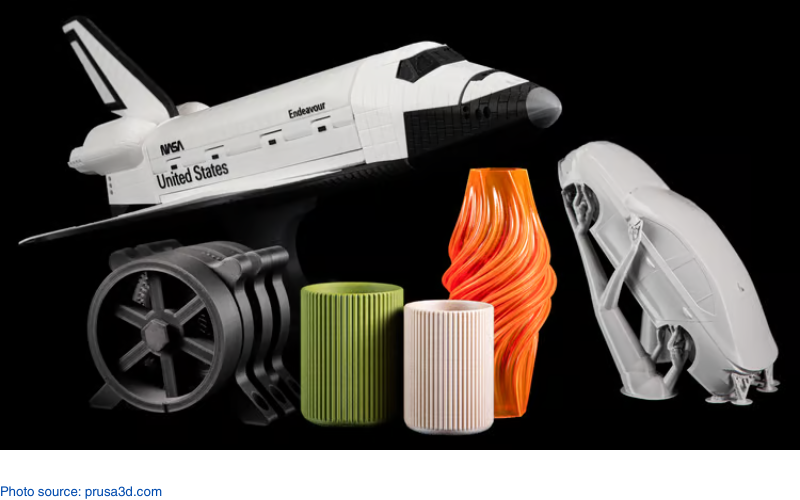
The Prusa XL packs in features you don’t usually find in printers this size. Its five-toolhead system doesn’t just let you print in multiple materials or colors—it swaps toolheads instantly, so there’s no wasted filament from purging between swaps. That means faster prints with less mess and lower costs.
The segmented heatbed only heats the sections it needs, keeping energy use low while still making sure large prints stick where they should. The loadcell sensor makes first-layer calibration automatic, so you don’t have to fiddle with settings. With Input Shaper and Pressure Advance, you can print at higher speeds without worrying about wobbles or rough edges. The Spool Join feature even switches spools automatically during huge prints, letting you create models up to 10 kg without stopping.
What really makes the Prusa XL special is how it handles tricky projects. You can combine flexible filaments, tough composites, and dissolvable supports in the same print. If you’re looking for a machine that can handle big, complex jobs while keeping things simple to run, the Prusa XL hits the mark.