Desktop Metal Studio System 2 Full Review
Desktop Metal has quickly become a leader in 3D printing since its founding in 2015. Known for their metal 3D printers, they’ve reshaped manufacturing by making the technology accessible and efficient. Using binder jetting, Desktop Metal has helped industries produce complex parts at a lower cost and faster speed. Aluminum 3D printers offer advantages like creating lightweight, durable parts for sectors like aerospace and automotive. This Desktop Metal Studio System 2 Full Review highlights how this system simplifies the metal printing process. It allows users to print precise metal parts in an office setting. With fewer manual steps, it makes 3D printing more available for companies, perfect for prototyping and small-scale production without needing a full industrial setup. This system delivers a streamlined solution to integrate metal printing into various workflows efficiently.
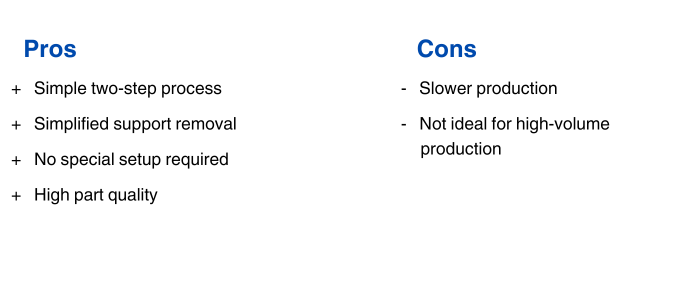
Design and Build Quality
The Desktop Metal Studio System 2 brings industrial metal 3D printing into an office-friendly package. Instead of using lasers and metal powders, it extrudes bound metal rods, which work like traditional filament printers. This makes the process safer and simpler for everyday environments.
With a build area of 300 x 200 x 200 mm, it has plenty of space for mid-sized parts. The system comes with two nozzle options: a high-resolution 250 µm nozzle for fine details and a 400 µm nozzle for faster prints. Changing materials is easy with a refillable cartridge system. The compact design, accessible hardware, and easy-to-use controls make it a practical choice for office setups.
The Technology of Studio System 2
The Studio System 2 uses a two-step process: print and sinter. It skips the solvent debinding phase, letting you go straight from printing to the furnace. Separable Supports technology simplifies part removal, allowing supports to be removed by hand.
The sintering furnace heats parts up to 1400°C, ensuring consistent heating. Parts come out with up to 98% density, comparable to casting. The Live Studio software automates the entire process, handling everything from scaling to support generation.
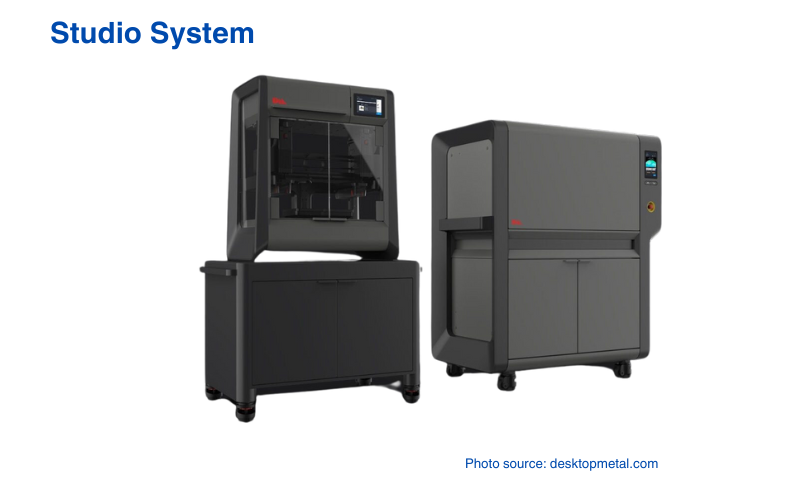
Key Features and Specifications
Key Features | Specifications |
---|---|
Two-step print and sinter process | Build Volume: 300 x 200 x 200 mm |
Bound metal rod extrusion | Print Nozzle Options: 250 µm, 400 µm |
Separable Supports technology | Peak Furnace Temperature: 1400°C (2552°F) |
No solvent debinding needed | Retort Size: 30 x 20 x 17 cm (12 x 8 x 6.7 in) |
Live Studio software | Environment: Argon, Argon + Hydrogen Blend, Inert Vacuum |
Refillable material cartridges | Compatible Materials: Stainless steel, Tool steel, Aluminum, Copper, and more |
Office-friendly |
The Desktop Metal Studio System 2 is a metal 3D printer for professionals who need high-quality parts. Its simple two-step process—print and sinter—removes the need for the traditional solvent debinding phase, making it easy and safe for use in office environments.
The system uses bound metal rods, similar to traditional filament printers, but designed for metal such as aluminum. This setup allows for complex geometries without dealing with metal powders. After printing, parts are easily removed thanks to the Separable Supports technology, so the post-processing is simple and quick. The system’s Live Studio software automates many aspects of the process, so you don’t need expert knowledge to get professional results. With an office-friendly design and easy-to-use hardware, it’s a practical solution for teams needing metal parts without the complications of traditional setups.
Comparisons
Studio System 2 vs. Studio System+
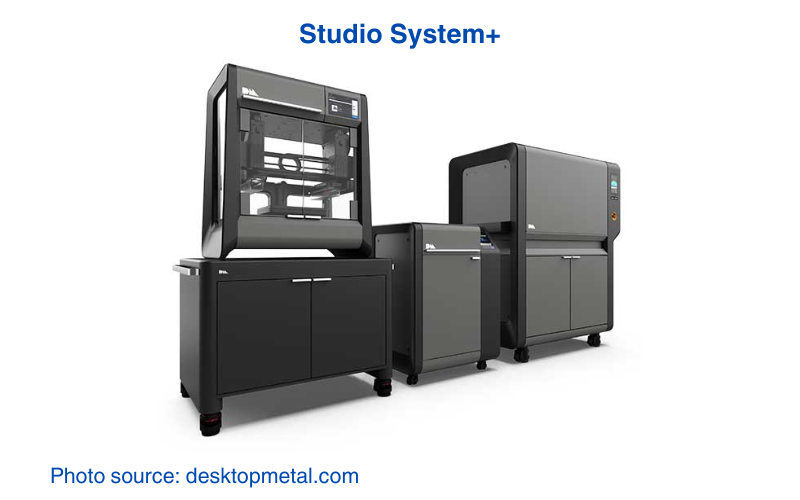
Comparing the Studio System 2 to the Studio System+, both are designed for professional use. However, the Studio System 2 improves upon the original Studio System+ in several key areas:
Processing Steps: The Studio System+ uses a three-step process that includes printing, debinding, and sintering. In contrast, the Studio System 2 eliminates the solvent debinding step, streamlining the workflow into a two-step process. This not only reduces complexity but also speeds up the production time, making it more efficient for office use.
Separable Supports: The Studio System 2 features upgraded Separable Supports technology, which allows supports to be removed by hand. The Studio System+ requires additional post-processing to remove supports, adding more time to the workflow.
User-Friendliness: The Studio System 2 is designed for even easier use, with its improved software and automated controls, allowing users to focus more on design rather than managing the machine. While the Studio System+ also supports office-friendly environments, the Studio System 2 takes it a step further by simplifying operations and minimizing manual intervention.
Studio System 2 vs. Shop System
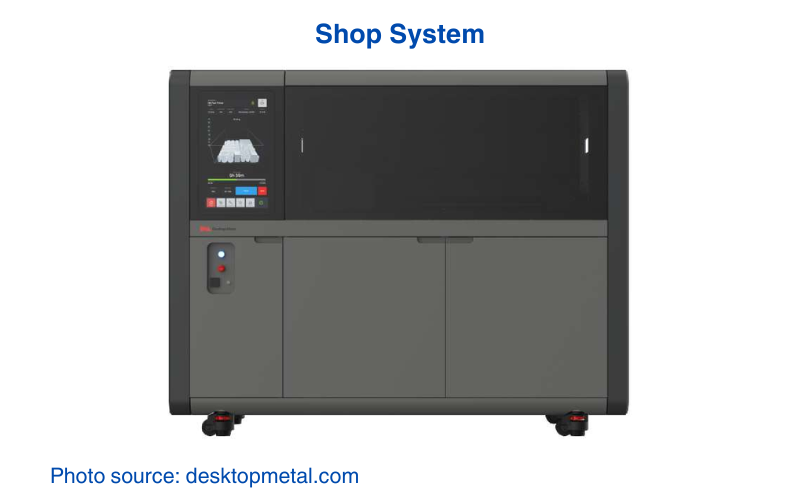
When comparing the Studio System 2 and Shop System, both are aimed at professionals, but the Studio System 2 excels with key improvements:
Production Scale: The Shop System is designed for higher-volume production, focusing on batch production of small, intricate parts. It uses binder jetting technology, making it ideal for manufacturers with high-output needs. In contrast, the Studio System 2 is about prototyping and low-volume production, for a more hands-off process for smaller teams.
Technology: The Shop System uses binder jetting, which allows for faster throughput but requires more post-processing steps like depowdering. The Studio System 2, with its bound metal rods, simplifies the process and eliminates the need for loose powders, making it safer and easier for office environments.
Material Handling: The Shop System focuses on higher production volumes, while the Studio System 2 handles complex, custom parts in smaller quantities.
Real World Applications
Companies can use the Studio System 2 in various industries to quickly produce metal parts with minimal effort. Its simple two-step process is perfect for prototyping, custom parts, and low-volume production. Here’s how it can be utilized:
Automotive
Professionals can use the Studio System 2 to prototype complex parts like engine brackets and turbocharger housings. Engineers can print these intricate designs quickly, test them, and refine the models before committing to full production. This process speeds up development and helps bring new designs to market faster.
Consumer Goods
Manufacturers of consumer products can use the Studio System 2 to create custom metal parts for prototypes or small product runs. It’s perfect for testing designs like metal housings for electronics or appliance components, letting teams refine their products before large-scale production.
Machine Design
Engineers designing machinery can benefit from the Studio System 2 when they need complex parts like gears or cooling channels. These intricate parts, often hard to machine, can be printed with precise internal features, reducing the need for assembly and improving performance.
Heavy Industry
In heavy industries like oil and gas, companies can use the Studio System 2 to create custom components for machinery, such as valve bodies or pipe connectors. These parts can be printed quickly to help replace critical equipment faster and reduce downtime.
Manufacturing Tooling
The Studio System 2 is ideal for creating custom tools and jigs used in manufacturing. Whether it’s a mold, fixture, or die, companies can print precise tools tailored to their needs. This helps manufacturers adapt quickly to production changes and keep their lines running smoothly.
Conclusion
The Desktop Metal Studio System 2 brings metal 3D printing, specifically aluminum 3D printers, into an office-friendly environment with a simple two-step process. By eliminating the need for solvent debinding, it streamlines production and makes metal printing more accessible to companies without requiring specialized facilities. With features like Separable Supports and bound metal rod extrusion, it’s easy to use and designed for efficiency. The Studio System 2 simplifies metal 3D printing, making it a practical choice for industries looking to innovate without the complexity of traditional manufacturing.